The model for the Powerbook 540 is: HOSIDEN MTFT HY4xxxxx27UA. It is a rather unusual panel, in that it was a 6-bit active matrix grayscale panel. The terminology for them at the time was "MTFT" standing for "Monochrome Thin Film Transistor". Unfortunately, at this time, Hosiden was not actually labeling real part numbers, they used a hybrid marking of part and manufacturing identifier. Three documented example of which I am aware are labels on the back of three different panels with the identifier "HY41403727UA", "HY4150BF27UA", & "HY4050FE27UA". Later Hosiden panels have distinct part number labels, as well as manufacturing identifiers. These panels are just about impossible to find outside of actual 540's and NOS mac repair parts. Attached below is a picture of the back of one of these panels.
All the Hosiden models are impacted. It's the seal. From what I understand this was not an uncommon issue with active matrix screens from this time period, apparently the art of sealing all the way down to a small molecular level hadn't been perfected yet.
It's almost certainly moisture since it is one of the few ways to explain why the images in the tunneled area remain on the screen even after power is removed, and even if the actual panel is removed from the system. The water interacting with the electrical element in the screen basically creates a capacitance effect, which continues to drive the screen in the absence of power being externally supplied, which is why the image is retained.
From all the work that has been done on this issue, time and temperature seem to be the critical factors. Temps of around 100C seem to work best, temps that people have tried below that, even for long period of time seem to work, but not as well as the results at 100C. 5 hours also seems to be a good benchmark for time. The only thing that can be done is determine the optimal time using trial and error. 100C or ever so slightly above any water trapped in the screen will want to become vapor, and as a result the vapor pressure will want to force the water vapor out of the nearest exit in the seal in order to expand to its proper volume, essentially acting as a driving force for the water to leave the screen. As for time, as
@bwinkel67 has shown, 5 hours works well, so the only things to do is go in both directions from that point until improvement stops or deterioration is seen to determine the best benefit vs. lowest risk. If any results below 5 hours at the predetermined temp quickly show they are inferior, then only more time needs to be tested. Same for more time, if it is quickly shown to be inferior, then only less time needs to be tested. Once the best time is found, the problem will have a best case treatment. After that the only work that needs to be done is to see if there is any way to reinforce the seal so water can't get back in again in the future, and if that can be accomplished, the problem will have a functional cure.
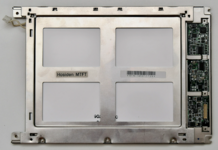